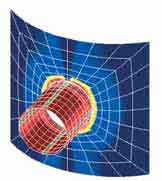
FE/PIPE
We provide the softwore to you in China as follows: please contact us
Click here | ![]() |
Finite Element Method for piping and vessels, FE/PIPE
FE/Pipe is a specialized finite element program developed for the piping and pressure vessel markets. It was created for the engineer who does not have time to work with a general-purpose FEA program. The primary focus of FE/Pipe development is to create a software package that quickly and easily allows modeling of complex structures using standard design geometries. FE/Pipe is a rapidly developing program, currently in use at 300+ companies analyzing simple nozzle geometries to the worldĄŻs largest vacuum tower. FE/Pipe Templates allow users to custom design and analyze job specific structures without the need of learning finite element theory. FE/Pipe is a feature rich software package and each month more customers discover how they can benefit the use FE/Pipe. The current FE/Pipe features are listed below:
Automatic calculation of allowable loads on nozzles. FE/Pipe generates a table of allowable loads
on any nozzle. The table includes the maximum individually and the maximum simultaneously
applied value of the load.
TRIFLEX interfaces that allow beam models to be read into the FE/Pipe beam analyzer and to interact
with FE/Pipe shell models.
A Standard lifting lug design calculator is included that recommends the size of lifting lug, the amount
of weld required and whether a brace or strong back is required to reduce the moments on the lug.
An axisymmetric/plane stress/plane strain model template which provides ASME code throughthickness
integration for calculation of section membrane and bending stresses.
An automatic fixed tube/tube sheet axisymmetric modeler that provides cross section stress
integrations, stress breakdowns according to primary or secondary stress calculations and autogenerated
angle, cross or tee shapes with optional radiuses. Also tube sheet allowable stress according
to ASME VIII div.1 App. A Finally, tube allowable loads according to TEMA RCB 7.24.
Input in the nozzle/plate, and cylinders-heads-plates template which allows the user to include the
effects of varying fluid elevations to properly simulate the effect of fluctuating pressure with depth,
this is required for simulating the Zick saddle analysis.
Rotation of databases allows all intersection models to be oriented in the global coordinate system
and included with other multiple nozzles or straight head bend models.
Input and analysis for simplified code guidance for plasticity and creep.
Harmonic excitation analysis of shell structures such as acoustic bottle vibration studies and wind
dynamic calculations.
Pressure stiffening analysis giving users the effect of pressure on SIFs (Stress Intensification Factors)
and stiffness at nozzle intersections.
AISC Structural steel database allowing users to model angles, double angles, channels and tee
geometries.
Symmetric and non-symmetric brick models that analyze flanges and bolts with external moments.
Spherical shell models that include options for non-penetrating tank legs and crown caps.
Shell modeling with an option to auto-connect beam endpoints to closest shell model.
Gussets can be added to reinforce nozzles for simulation of plastic rib reinforced nozzles and mixer
nozzle supports.
Header, shell and pad modeling with alternate plate meshing to improve large plate constructions,
SIFs and stiffness for run moments through the header and individual close plate surface joining.
Oval miter section modeling options and straight edge miter sections.